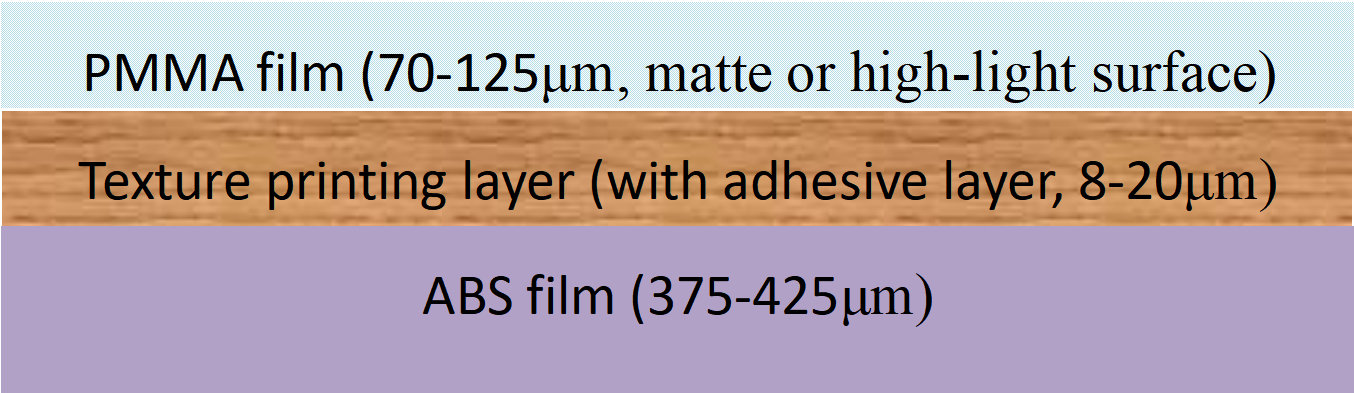
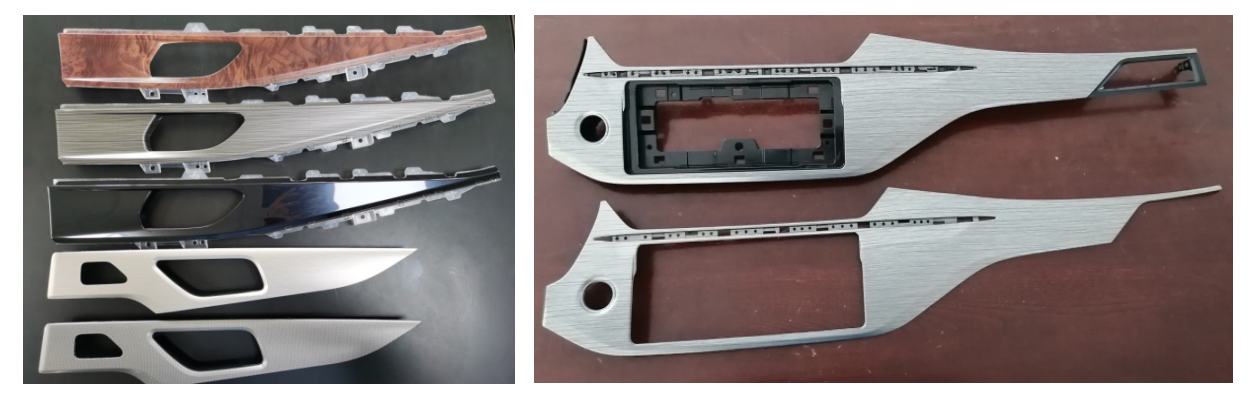
Item | Test standard or Test method | Test Data |
Thickness | Micrometer | 0.5±0.030mm |
Hot Stretch | Heat to 110-120℃ to soften and then stretch | ≥200% |
Appearance | Eye Survey | No defects on film surface such as spelling, sand holes, bubbles, cracks, wrinkles, scratches, pattern deformation and so on. No breakage, layering, color change, fine lines or cracks of texture. |
Adhesion | Grid Test | No shedding |
High Temperature Thermal Aged | Place it in a high temperature oven for 168 hours and at room temperature for 2 hours, 85-100℃. | No obvious loss of light, discoloration, bubble, shedding, cracking and other changes, adhesion level 0 |
Alternating High and Low Temperatures | High and low temperature cycle resistance Cycle between -30℃ and 90℃ according to industry test standard | No obvious loss of light, discoloration, bubble, shedding, cracking and other changes, adhesion level 0 |
Color Fastness | Sample size 25mm×150mm, 2 pieces of cotton cloth in 50*50mm wrapped in the friction head, apply force of 9N, a cycle per second, total 10 cycles of friction, compare the white cloth after rubbing with the original cloth, evaluate the staining grade of white cloth according to GB251 | Dry rub: No color scratch marks, stained color level 4. Wet rub: No obvious swelling, dissolution, stickiness, foaming, wrinkling and other changes, stained color grade 4 |
Taber Abrasion Resistance | Choose sample template in size 100mmx100mm, put it on the Taber Abraser, using CS10 grinding wheel, 5N (500GF) load rub sample at least 600 times at the speed of 60±2rpm. | No wearing out the printing effect layer |
Chemicals resistance | Industry/Enterprise Standard | No obvious swelling, dissolution, stickiness, foaming, wrinkling and other changes, no shedding after adhesion test through grid method . |
Cosmetics Resistance | Industry/Enterprise Standard | Slight improvement in luster, no obvious discoloration, no shedding after adhesion test through grid method . |
Low Temperature Resistance | Industry/Enterprise Standard | No obvious loss of light, discoloration, bubble, shedding,cracking and other changes, no shedding after adhesion test through grid method . |
Flammability | GB 8410 | ≤100mm/min(injection molding 2mmABS test) |
No additional mold cost can realize excellent lot to lot colour control,low VOC emissions and reduction of waste.
(1) Thermoforming (1.1) Equipment is required like a forming, trimming and molding equipment. (2)Storage (2.1) INS films should be stored under normal operating conditions. Boxes containing rolls of INS films should be stored in a horizontal position. This material should not be stored outdoors, in places of high humidity or where extreme temperatures can be attained. Temperatures below the freezing point and over 35°C should be avoided. (2.2)If the roll of film is to be stored again, it must be kept wrapped in the moisture vapor barrier with desiccants inside. The wrap needs to be sealed at the seam with a PET tape, and then sealed at the core end with a core plug or something similar. (2.3)Recommended storage is 25°C or cooler at the lowest humidity level possible. Re-dry after 5-6 months. (2.4)It is recommended to pre-dry sheets 2 days at 70℃, full unwrapped rolls min. 48~72 hours at 60℃ in a circulation oven. (3)Forming (3.1)Slow heating of the film, preferably heating the film back side targeting a sheet temperature of 120℃~145℃measured by temperature labels.it depended on the different part and film type. (3.2)Operation in clean room is preferred. (4)Trimming (4.1)It is recommended to use laser cutting, or die cutting, generally die cutting.When trimmed, ensure that the material is not damaged, no dust, dirt pollution,trimming scraps on the surface. (4.2)To avoid surface damage we recommend the following operations: (4.2.1)Do not pile on top of each other without soft tissue or cloth between each part. (4.2.2)Have all personnel wear soft or latex gloves. (4.2.3)To avoid dust pick-up or contamination we recommend the use of anti-static devices specifically designed for clean room atmospheres. (5)Insert molding (5.1)No special equipment is necessary when processing INS film. Existing molding equipment can be used; however, moulds should be made or modified to accept the film in the cavity. Further recommendations: (5.2)The temperature of the diaphragm inserted into the mold cavity should be 30-50°C. (5.3)Film friendly gating to prevent wash out of color and or graphics. (5.4)Resin temperature as recommended by the resin supplier.